In recent years, the meatpacking industry has witnessed a significant transformation driven by the integration of robotics and automation into production processes. As technological advancements revolutionize traditional methods of meat processing, robots are increasingly assuming roles once performed by human workers. In this article, we explore the implications of this shift, examining the drivers behind the adoption of robotics in the meatpacking industry and its impact on workers, efficiency, and food production. The Rise of Automation: Robots Transforming the Meatpacking Industry.
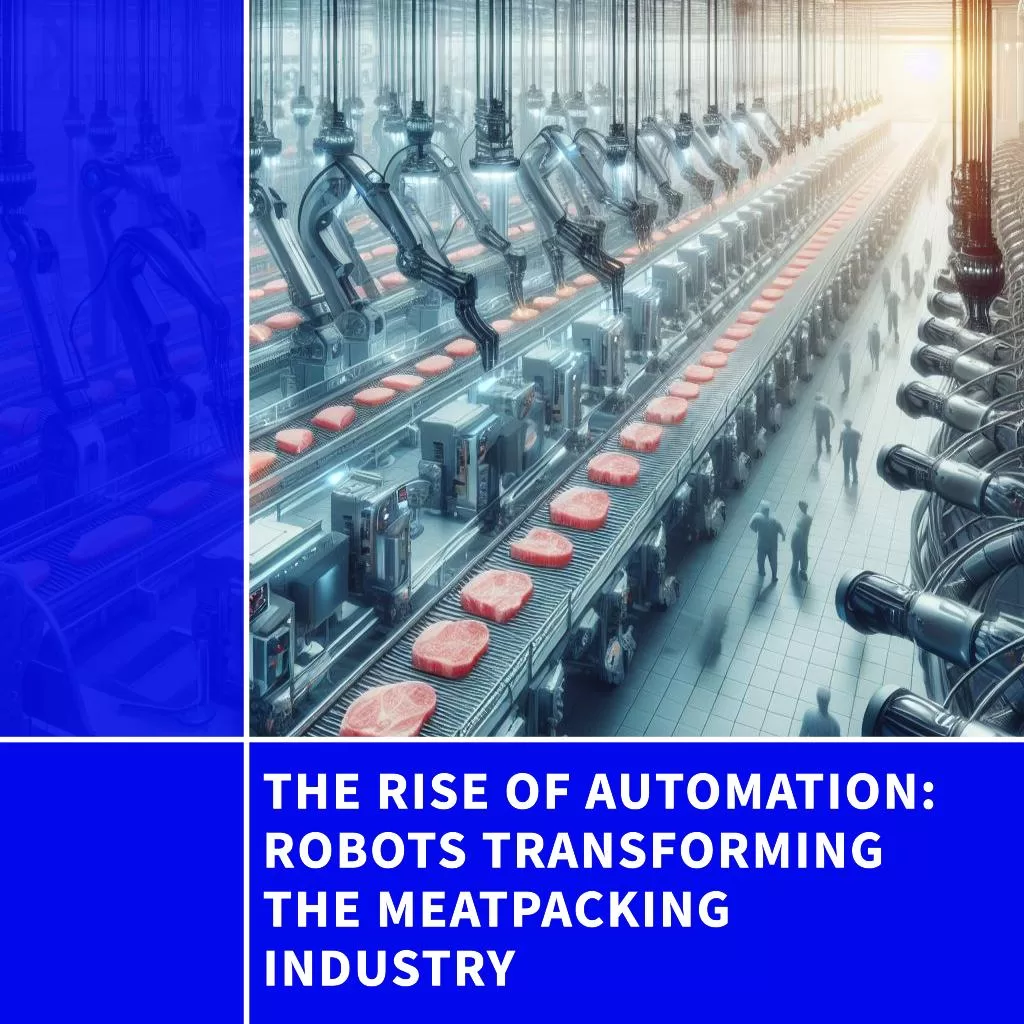
Automation Revolutionizing Meatpacking:
Robotic automation is revolutionizing the meatpacking industry, offering a range of benefits including increased efficiency, enhanced food safety, and cost savings. Robots equipped with advanced sensors, vision systems, and cutting-edge software can perform tasks such as carcass cutting, trimming, and packaging with precision and consistency, reducing human error and improving product quality. Moreover, robotic systems can operate continuously without fatigue or breaks, leading to higher productivity and throughput in meat processing plants.
Addressing Labor Challenges:
The adoption of robotics in meatpacking comes at a time when the industry faces significant labor challenges, including workforce shortages, high turnover rates, and concerns about worker safety and welfare. By automating repetitive and physically demanding tasks, robots can alleviate the burden on human workers, reducing the risk of injuries and ergonomic strain associated with manual labor. Moreover, robots can operate in environments with extreme temperatures and sanitary conditions, mitigating health and safety risks for workers.
Improving Food Safety and Quality:
Food safety is a top priority in the meatpacking industry, with strict regulations and standards governing the production and handling of meat products. Robots play a crucial role in ensuring compliance with food safety protocols by minimizing the risk of contamination and cross-contamination during processing. Automated systems can sanitize equipment, monitor hygiene practices, and implement stringent quality control measures to detect and remove defects or contaminants, enhancing consumer confidence in the safety and integrity of meat products.
Enhancing Efficiency and Productivity:
Automation offers significant opportunities for improving efficiency and productivity in meatpacking operations. By streamlining workflows, reducing cycle times, and optimizing resource utilization, robots can increase throughput and output while lowering production costs. Automated systems can perform tasks at a consistent pace and precision, eliminating bottlenecks and delays associated with manual labor. Moreover, real-time data analytics and machine learning algorithms enable continuous optimization and process improvement, driving operational excellence and competitiveness in the meatpacking industry.
Reshaping the Workforce:
While the adoption of robotics in meatpacking holds promise for efficiency and safety, it also raises questions about the future of the workforce. As robots assume more tasks traditionally performed by human workers, the nature of jobs in the meatpacking industry is evolving. Workers may need to acquire new skills and competencies to operate and maintain robotic systems, leading to shifts in job roles and responsibilities. Moreover, the integration of automation may create new opportunities for collaboration between humans and robots, fostering a hybrid workforce model that combines human ingenuity with machine efficiency.
Conclusion:
The integration of robotics and automation is revolutionizing the meatpacking industry, reshaping production processes, and redefining the workforce. By harnessing the power of technology, meat processors can enhance efficiency, improve food safety, and address labor challenges while maintaining competitiveness in a rapidly evolving market. As robots continue to take on a greater role in meatpacking operations, stakeholders must embrace innovation, invest in training and development, and collaborate to realize the full potential of automation in shaping the future of food production.